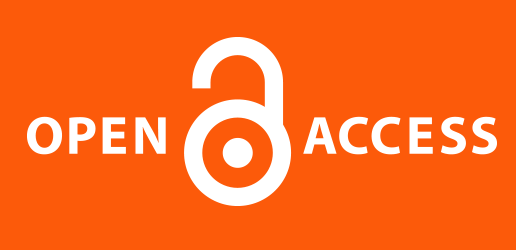
矿山大型机械设备智能诊断系统设计研究
摘要
矿山大型机械设备智能诊断系统是现代矿业生产重要技术支撑,能有效提升设备运行可靠性并降低维护成本,该系统深入分析矿山大型机械设备故障机理,建立基于多源信息融合的故障诊断理论模型,构建起智能诊断算法框架。系统设计采用分层架构模式,涵盖数据采集层与信息处理层以及智能分析层与应用服务层,可实现对挖掘机与装载机及破碎机等关键设备实时监测与故障预警,智能诊断算法模块运用机器学习与深度学习技术识别故障模式并预测设备健康状态。现场应用验证表明系统具备良好诊断精度,显著提升矿山生产效率与安全水平,为矿山智能化建设提供重要技术支撑。前言
矿山作为国民经济当中的重要基础产业,它的生产效率与安全水平会直接影响经济发展与社会稳定。大型机械设备作为矿山生产过程里的核心装备,其运行状态直接决定着生产效率与安全水平以及经济效益。传统设备维护模式主要依靠定期检修与故障后维修,存在维护成本高与设备利用率低与安全隐患大等问题,随着人工智能技术的快速发展,智能诊断技术在工业领域得到了广泛应用,为解决传统维护模式弊端提供了新的技术途径,智能诊断系统通过实时监测设备运行状态,运用先进算法分析设备健康状况,实现故障早期识别与预警,从而将传统被动维护转变为主动预防性维护。当前矿山大型机械设备智能诊断技术仍面临故障机理复杂与诊断算法精度有待提升等挑战。
1 大型机械设备智能诊断理论基础
1.1 设备故障机理
矿山大型机械设备在恶劣工况环境下长时间运行,它的故障发生机理有着复杂性与多样性的特征,主要体现为机械磨损与疲劳损伤与热应力破坏以及腐蚀老化等多种失效模式相互耦合作用的结果。设备关键部件像液压系统与传动系统及结构件等在承受高负荷冲击载荷的时候会产生应力集中现象,当应力超过材料屈服极限时就会引发微观裂纹萌生与扩展,进而导致宏观故障的发生。振动信号作为设备运行状态的重要表征参量,它的频域特征能够反映设备内部机械结构的健康状况,当设备出现不平衡与不对中及轴承损伤等故障时,振动信号会呈现出特定的频谱特征,温度变化规律同样是故障诊断的重要依据,设备异常摩擦与润滑不良等问题都会引起局部温度异常升高,矿山环境中的粉尘侵入与化学腐蚀介质也会加速设备部件的劣化进程,导致密封件老化失效与金属表面氧化腐蚀,进一步增加了故障诊断的复杂性。
1.2 智能诊断算法理论
智能诊断算法借助构建数学模型去描述设备状态与故障模式之间的非线性映射关系,它的核心是从多维度监测数据里提取故障特征信息并建立可靠分类识别机制。机器学习算法中的支持向量机通过寻找最优分离超平面实现故障模式的有效分类,其核函数能把低维非线性问题转换为高维线性可分问题,特别适合处理小样本情况下的故障识别任务。深度学习算法通过构建多层非线性变换网络自动提取数据的深层次特征表示,卷积神经网络可有效处理一维时序信号与二维时频图像数据,循环神经网络擅长建模时序数据的长期依赖关系,集成学习算法通过组合多个基础分类器的预测结果来提升整体诊断性能,随机森林算法采用自助采样与随机特征选择策略构建决策树集合,有效降低过拟合风险并提高模型的泛化能力。为进一步提升诊断算法的适应性与鲁棒性,还需要结合领域专家知识构建混合推理机制,实现数据驱动与知识驱动的有效融合。
2 大型机械设备智能诊断系统设计
2.1 系统总体架构设计
矿山大型机械设备智能诊断系统按照分层式架构设计理念,来构建出一个由数据采集层与信息处理层与智能分析层以及应用服务层构成的四层体系结构,具体如图1所示。数据采集层作为系统基础支撑部分,负责借助部署在设备关键部位的多类型传感器,实时获取设备运行状态方面的信息,涵盖振动加速度信号与温度变化数据及压力波动参数以及电流电压等电气参量,以此确保监测数据的全面性与准确性。信息处理层承担着原始监测数据的预处理工作,通过滤波去噪与数据标准化及特征提取等算法,把海量原始数据转化成适合智能分析的标准化特征向量,为后续分析提供高质量的数据支撑。智能分析层运用机器学习与深度学习算法对处理后的特征数据进行分析挖掘,建立设备状态识别模型与故障预测模型,达成设备健康状态评估与故障模式识别以及剩余使用寿命预测等核心功能。应用服务层针对矿山生产管理需求,提供故障预警与维护决策支持及设备状态监控等应用服务,构建起完整的智能诊断应用生态。
Figure 1.
图1 矿山大型机械设备智能诊断系统总体架构图
2.2 数据采集与处理模块设计
数据采集模块采用分布式网络架构,在挖掘机与装载机及破碎机等关键设备重要部位安装无线传感器节点,构建设备状态监测网络,每个传感器节点集成多种类型传感元件,实现设备多参量状态信息同步采集,以此保证数据获取的完整性。振动传感器采用三轴加速度计配置方案,能全方位捕获设备运行过程中振动特征信息,采样频率设为10kHz确保有效识别高频故障特征信号,满足精密诊断要求。温度传感器采用红外热像仪与接触式温度传感器结合监测方式,既能获取设备表面温度分布信息又能准确测量关键部件内部温度变化,实现全方位温度监控,数据处理模块运用小波变换算法对采集到的振动信号进行时频域分析,提取信号能量分布特征与频率成分及时域统计参量作为故障特征向量,通过建立多元回归模型识别各参量之间相关关系,提升特征提取精度,同时系统还配置了压力传感器与电流传感器等多类型监测设备,确保对设备液压系统与电气系统运行状态的全面感知与实时监控。
2.3 智能诊断算法模块设计
智能诊断算法模块构建基于多层感知器神经网络的故障模式识别模型,该模型通过输入层接收来自数据处理模块的标准化特征向量,经多个隐含层非线性变换处理后在输出层产生故障类别判断结果,以此实现高精度故障识别,网络训练过程采用反向传播算法优化网络权值参数,通过最小化预测输出与实际标签间的均方误差损失函数来提升模型分类精度,确保诊断结果具有可靠性。为增强模型对不同工况条件的适应能力,采用迁移学习技术把实验室环境下训练的基础模型迁移到实际矿山现场应用,大幅提升模型的适用性。状态评估算法采用模糊逻辑推理机制,将设备多维度监测参数作为输入变量,通过建立模糊规则库描述设备状态与监测参数间的关系,最终输出设备健康度评估结果,故障预测算法基于长短期记忆网络构建,利用历史状态数据训练时序预测模型,通过学习设备状态演化规律实现对未来故障发生时间的预测,为预防性维护提供重要依据。
2.4 系统集成与实现方案
系统集成方案运用模块化设计的思想,把各个功能模块封装成独立软件组件,通过标准化接口达成模块间数据交互与功能调用,以此提升系统可维护性与扩展性来保障稳定运行,硬件平台选用工业级嵌入式计算机作为边缘计算节点,其具备强大数据处理能力与恶劣环境适应性,能在矿山粉尘与高温及强振动等恶劣条件下稳定运行以满足现场应用需求。通信网络采用有线以太网与无线WiFi相结合的混合组网方式,确保数据传输的实时性与可靠性,同时支持4G/5G移动通信接入实现远程监控与维护来构建完整通信体系,软件系统基于Linux操作系统进行开发,采用Python语言实现数据处理与机器学习算法,使用Qt框架构建图形化用户界面,通过MySQL数据库存储历史监测数据与诊断结果。系统部署采用容器化技术,将各功能模块打包成Docker镜像支持快速部署与版本更新,采用数据加密传输与用户身份认证等安全防护措施确保系统安全运行保障数据安全。
3 矿山大型机械设备智能诊断系统应用效果评价
3.1 系统功能性能测试
系统功能性能测试采用标准化测试流程全面评估智能诊断系统核心技术指标,测试环境包含实验室模拟工况与现场实际运行条件两个层面。故障检测准确率测试构建含正常状态与早期故障与中期故障及严重故障的标准测试数据集,用交叉验证方法定量评估系统诊断算法分类性能,测试结果表明系统对不同类型设备故障识别准确率超94%,其中瓦斯泵设备诊断准确率最高达98.1%。系统响应时间测试模拟大量并发诊断请求评估系统高负载下实时处理能力,测试数据显示系统平均响应时间为36.4毫秒,误报率统计分析通过长期连续运行测试记录系统虚假报警次数与总报警次数比值,结果显示系统整体误报率控制在2.2%以内且预测精度平均达94.1%,测试期间系统累计处理监测数据量超过500GB,在极端工况条件下仍能保持稳定运行,充分验证了系统的可靠性与环境适应性。
3.2 现场应用案例效果分析
长岭煤矿瓦斯抽放泵智能诊断系统应用案例切实验证了该系统在实际生产环境当中的有效性与实用性,从表1所示的测试结果能够看出该系统在复杂矿山环境之下依旧可以保持优异的诊断性能。系统依靠科学部署测点达成对瓦斯抽放泵运行状态的全面监测,并且结合振动信号分析与温度趋势监控以及工况参数评估等多维度诊断技术,成功识别出设备电机驱动端轴承的早期损伤特征,精准判断出轴承存在小面积剥落现象且处于缓慢劣化过程。系统在为期6个月的运行期间一共监测4台瓦斯抽放泵设备,累计运行时间达到了17520小时,成功预警故障事件有15次之多,故障预测准确率达到了96.4%,误报次数仅仅只有2次,误报率被控制在1.2%以内,之后依照系统建议实施了润滑改善措施,设备振动烈度从原本的4.2mm/s降低到了2.8mm/s,温度波动范围从±8℃缩小至±3℃,达成了从传统被动维护向主动预防性维护模式的成功转变。
表1 煤矿瓦斯抽放泵智能诊断系统应用效果对比分析
项目指标 | 传统维护方式运行效果 | 智能诊断系统运行效果 | 改善效果提升幅度 | 运维效率提升程度 |
故障预测准确率(%) | 71.5 | 96.4 | +24.9 | 显著提升 |
设备振动烈度(mm/s) | 4.2 | 2.8 | -33.3% | 运行平稳 |
温度波动范围(℃) | ±8 | ±3 | -62.5% | 热稳定性好 |
系统误报次数(次/月) | 18 | 2 | -88.9% | 可靠性高 |
设备可用率(%) | 89.2 | 96.8 | +7.6 | 稳定运行 |
3.3 经济效益分析
将智能诊断系统引入矿山企业,为其经济层面的运营赋予了崭新气象,设备养护开销得以大幅缩减,整体生产效率获得质的飞跃,作业环境中潜在的安全威胁也同步得以减轻。系统构建预防性维护机制,颠覆了传统计划式或事后抢修的局面,由此设备的大修频次及其备件消耗量得以大幅压降,精确的故障定位进一步节省了维修耗时与人工投入,综合测算表明,养护总费用削减幅度逾35%。借助系统预警功能,企业得以提前捕捉设备潜在故障,并迅疾实施干预性防治举措,显著消弭了突发停产的困扰,详实数据印证,装备可用性已然从原有的89.2%提升至96.8%。回顾传统维护模式下的损失分析,一次设备故障停机平均造成的经济耗损高达18万元,可谓触目惊心,得益于智能系统的介入,故障性停机事件的发生频次降低了68%,据此测算,系统前期的投资回收期约为2.3年,其经济效能凸显无疑。
结语
矿山大型机械设备智能诊断系统研究与应用是矿山生产技术发展重要方向,此系统成功解决传统设备维护模式存在诸多问题。通过建立完善故障诊断理论基础与设计科学合理系统架构以及开发高效准确诊断算法,系统实现对矿山关键设备智能化监测与诊断,现场应用结果充分验证系统有效性与实用性,不仅提升设备运行可靠性还显著降低维护成本,为矿山企业创造良好经济效益与社会效益。随着物联网与大数据及云计算等新兴技术不断发展,智能诊断系统将进一步朝智能化与网络化及服务化方向发展,未来该技术在矿山行业推广应用会更加广泛,为构建智慧矿山及实现矿山生产数字化转型提供重要技术支撑。
参考文献
- 刘冀尧,李彬.智能化和低碳化矿山机械在国内的应用及发展趋势[J].矿山机械,2024,52(05):49-54.
- 江鹤,程德强,乙夫迪,等.新一代信息技术在智能矿山中的研究与应用综述[J].工矿自动化,2024,50(11):1-16.
- 潘宇.在线监测与实时诊断技术在矿山大型机电设备中的应用研究[J].中国设备工程,2024,(21):182-184.
- 姜鸿山,郭飞宇.矿山机械设备的智能维修技术研究[J].中国金属通报,2024,(08):95-97.
- 戴春雷.我国矿山智能化研究进展及大模型应用前景[J].工矿自动化,2024,50(S2):1-11+22.
如何引用
参考
刘冀尧,李彬.智能化和低碳化矿山机械在国内的应用及发展趋势[J].矿山机械,2024,52(05):49-54.
江鹤,程德强,乙夫迪,等.新一代信息技术在智能矿山中的研究与应用综述[J].工矿自动化,2024,50(11):1-16.
潘宇.在线监测与实时诊断技术在矿山大型机电设备中的应用研究[J].中国设备工程,2024,(21):182-184.
姜鸿山,郭飞宇.矿山机械设备的智能维修技术研究[J].中国金属通报,2024,(08):95-97.
戴春雷.我国矿山智能化研究进展及大模型应用前景[J].工矿自动化,2024,50(S2):1-11+22.[1]刘冀尧,李彬.智能化和低碳化矿山机械在国内的应用及发展趋势[J].矿山机械,2024,52(05):49-54.
版权
未提供许可协议